Hygiene has become not just desirable, but a key indicator that passengers are looking for when flying. Inevitably though, as traffic picks up, the intensive cleaning regimes adopted by airlines in the first line of defence against coronavirus will impact aircraft turnaround times and schedule demands.
Instead, the materials technologists and cabin specialists are now working on surfaces and products to support airline requirements for hygiene and increased efficiency, while also reducing the need for harsh cleaning regimes. In the longer term, this will lead to aircraft interiors with in-built resistance against pathogens.
Surface coatings to cut down cleaning times
While new cabins may not be in current plans for many airlines, some are already deploying surface treatments with anti-microbial technology. Surfaces such as seats, tray tables, overhead bins and lavatories across United Airlines’ entire mainline and express fleets are being treated weekly with the surface de-contaminant Zoono Microbe Shield. The spray treatment, which is part of the airline’s United CleanPlus programme, bonds to surfaces and ruptures the cell walls and membranes of microbes that come into contact with it.
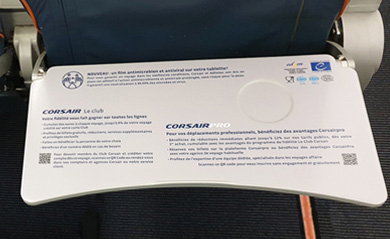
Last autumn, Corsair began progressively equipping their tray tables in the aircraft with a protective film incorporating antibacterial and antiviral properties. The film, developed by ADHETEC in partnership with Pylote, provides an immediate and stable microbial decontamination action without loss of effectiveness for four years and protects the tables from aggressive disinfectant products.
Collaboration leads to new solutions
A sense of what is possible in the future can be glimpsed in some recent collaborations. Tapis Corporation, SIMONA Boltaron and Molon Labe Seating joined forces last summer to demonstrate a solution for safer travel. The starting point was Molon Labe’s S2 seat, which features a fresh air vent in the one-sided headrest that can also be rotated to form a physical barrier between passengers.
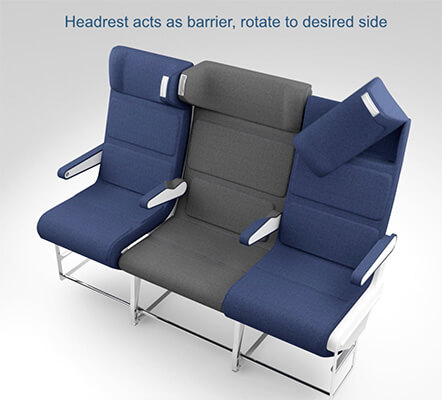
The seat back, seat pan, armrests and headrests are covered in Promessa Ultrafabric from Tapis, which includes antimicrobial silver ion technology in the top skin. Boltaron’s 9815N FAR-rated material was then used for the thermoformed seat backs, which has an antimicrobial treatment as standard.

“Between [all of] us, we had something like greater than 90% of the seat’s surfaces covered in antimicrobial technology without compromising passenger comfort or experience,” reports Matthew Nicholls, Sales Director at Tapis. He adds that Tapis and its partner Ultrafabrics have seen the addition of Promessa AV to JetBlue Airways, Spirit Airlines and American Airlines fleets in the past 12 months.
Surfaces that self-clean
Safran Cabin has teamed up with 3M to help design cleaner aircraft cabin interiors as part of Safran’s ‘Travel Safe’ initiative. Their current focus is developing a residual antimicrobial coating that can be sprayed or wiped on to make a surface continuously antimicrobial for at least 30 days, claiming the ability to kill 99.9% of viruses and bacteria in 10 minutes.

“It is our goal to create a ‘self-disinfecting’ interior using this technology,” says Nathan Kwok, Vice President Marketing at Safran Cabin. Their planned next step will be to make antimicrobial and easy-clean properties a permanent feature of the interior surface. Kwok explains: “We are currently studying ways to integrate our polymer into the huge variety of materials, colours, and textures that exist today. The goal is that every surface is antimicrobial, without sacrificing the richness of the colour and texture palette.”
Resistance to disinfectants
Matthew Nicholls at Tapis also notes that materials and surface coatings will need to have resistance to disinfectants if they are going to last into the future, with requirements from airlines evolving to include the ability to clean surfaces with a wide variety of aviation-approved disinfectants.
As an example, American Airlines’ recent 737-800 upgrades included cabin dividers from Jamco America covered in Tapis 9-series Ultraleather, which has antimicrobial silver ion technology embedded in the surface layers. The finish is resistant to cleaning materials used in foggers and hydrostatic sprayers while still being able to be cleaned with alcohol, quaternary ammonium, bleach and hydrogen peroxide-based cleaners without damage.
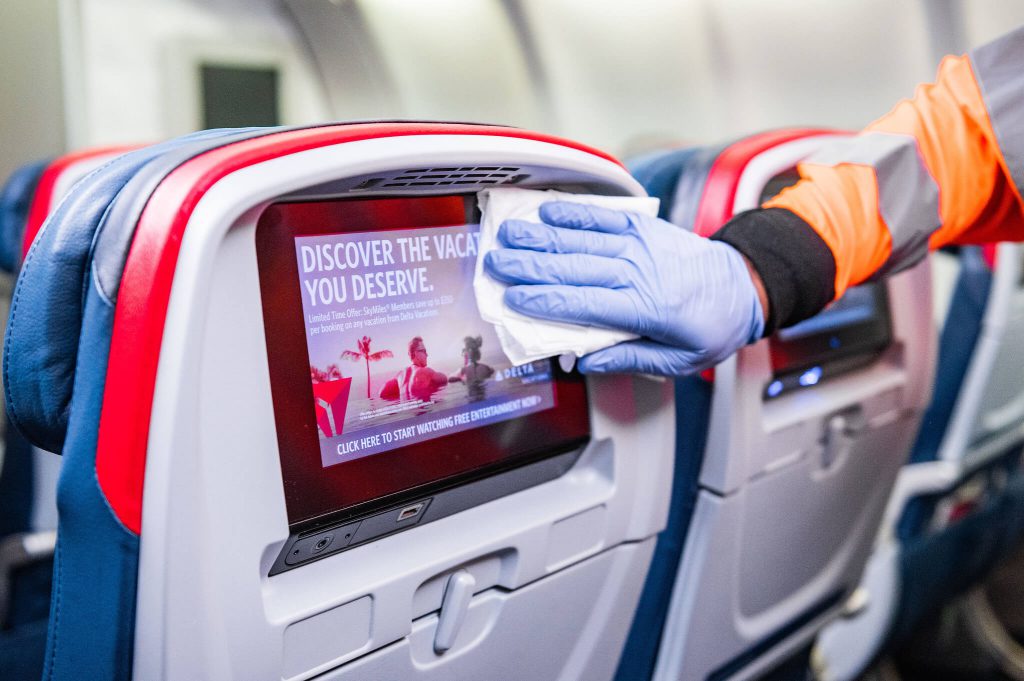
Other suppliers also highlight the robustness of anti-pathogenic products against contaminants and cleaning agents. For example, high-touch interior replacement parts, such as tray tables and lavatory seats, from Aereos Interior Solutions are certified greater than 99.8% effective against microbes, while also protecting the surface finish.
Removing chemicals from cleaning
Once the cabin’s fixtures and fittings are covered with antimicrobial technology, a review of cleaning regimes will be needed. The elimination of chemicals in aircraft cabin cleaning is a key goal for Muirhead Leather. Its Active Hygiene Leather has built-in antimicrobial self-cleaning properties thanks to permanently integrating Polygiene® ViralOffTM into the leather during the production process, breaking down bacteria that cause odours as well as viruses to over 99% within two hours.
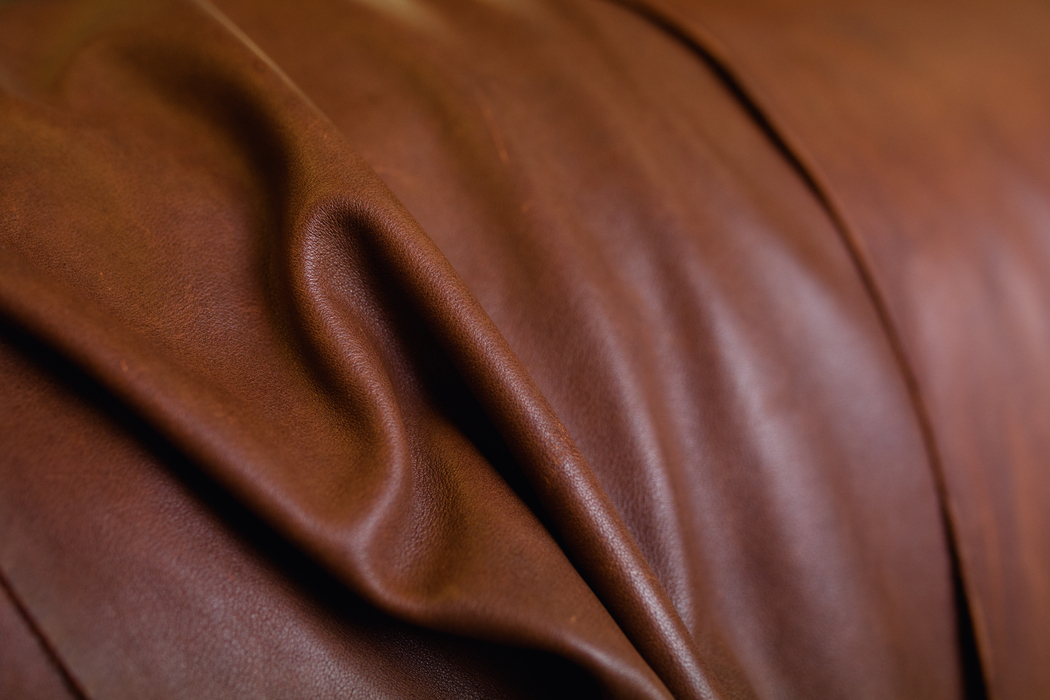
Myles Hobbs, Head of Sales (Aviation) EMEA and The Americas recommends maintaining its product with only pH-neutral soap and sparing use of water. “During our 7–10-year product life cycle, there is no need to use any lotion, potions, or chemicals,” he says.
Still some challenges to overcome
Incorporating antimicrobial technology into products has challenges. Nicholls says that getting silver content just right is a science in its own right. He goes on to explain that you have to have enough silver particles to provide a safe surface, but as the quantity increases, they can become hard to distribute evenly, also increasing weight and decreasing durability.
Defining a new regulatory paradigm around antimicrobial materials will also be tough, according to Kwok. “Most cleaning and disinfecting guidance documents were written around chemicals that worked while wet, and never envisioned that the surface itself was also the disinfectant. So, now we need to decide as an industry, what level of efficacy is sufficient to declare a surface self-disinfecting? This requires a lot of collaboration across different regulatory agencies because consistency will be important in building confidence.”
Nicholls concurs: “We need to make sure that we’re not compromising other key aspects of the fundamental passenger experience in our rush to solve the COVID issues.”
Hidden benefits of surface coatings need clear messaging
Communicating the hygiene and safety benefits of cleaning regimes to passengers is already part of airline strategies to reassure people that it is safe to fly. It is key when the hygiene technology is embedded in the interior and, as Kwok notes, works invisibly. “There are a variety of ways to do this, including colour and graphical indications on the surface itself, as well as messaging directly to the passengers during the safety briefing or even during the booking process,” he says.
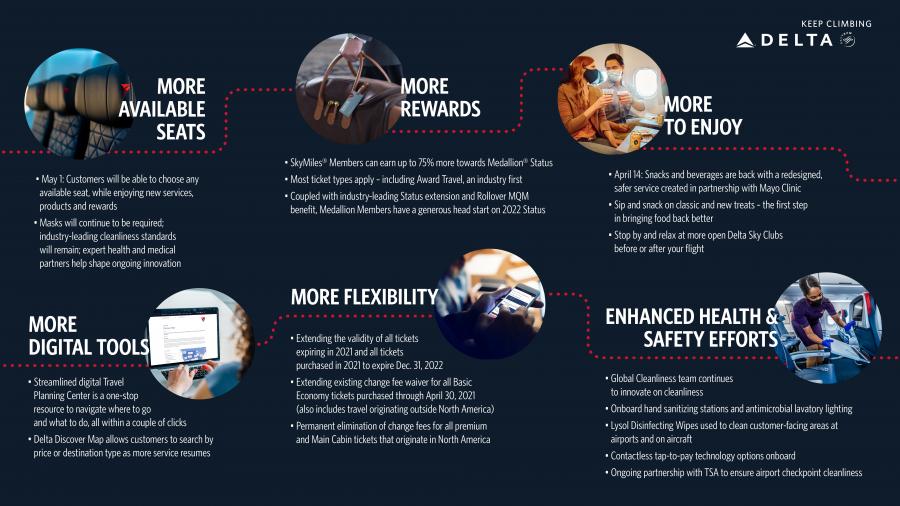
“Our first goal is safety, but also a more relaxed travel experience. We hope that when passengers see the Safran logo, they have confidence that surface does not need that extra squirt of spray cleaner they brought with them because the technology inside the surface works even better.”
Airline requirements for hygiene solutions will evolve as air travel recovery gets underway. In the short term, regular surface treatments would seem to be the natural solution. In the longer term, more innately hygienic interiors mean that there will be improved and potentially less costly cleaning regimes. Ultimately, consistent standards for antimicrobial technologies in aircraft will need to be established to continue to build confidence in air travel.