Aircraft seating is one of many areas of the aviation industry’s decarbonisation initiatives and its modest profile belies its importance. Seating is a microcosm of the business as a whole and what’s happening at the airline seat level informs how other segments of the aviation interiors industry might approach the climate emergency.
Transitioning to sustainable aviation fuels and innovating alternative power sources will inevitably create the initial big wins by reducing the direct emissions of aircraft. But there are even more significant long-term reductions to be made by lowering emissions that the airline is indirectly responsible for – and this is where seating and the cabin interior fit into the picture.
According to estimates by aviation analytics specialist Cirium, total CO2 emissions from scheduled passenger flights worldwide totalled 804m tonnes in 2019. Emissions fell dramatically during the covid pandemic, but reached 728m tonnes in 2023.
This year, Cirium projects that emissions will exceed the 2019 high by around 10m tonnes – based on published airline schedules.
Cirium’s Senior Director, Market Development, Andrew Doyle explains: “The highest ever single month for emissions was July 2019 and this previous high-water mark is currently expected to be exceeded in July 2024.”
He adds: “Having said that, overall efficiency has improved as airlines progressively take delivery of latest technology aircraft. Cirium expects a decline in CO2 per available seat kilometre of just under 4% for 2024 compared with 2019. However, this of course highlights the scale of the task the industry faces to reach ‘net zero’ by 2050.”
The consensus vision
What then does sustainability look like for the players in the seating sector? There is a broad consensus from aircraft manufacturer to designers, from seating OEM to seat cover specialist, that reducing weight is a big first step, but shifting to regenerative and circular models for manufacturing and doing business is where far greater gains can be derived over the longer term.
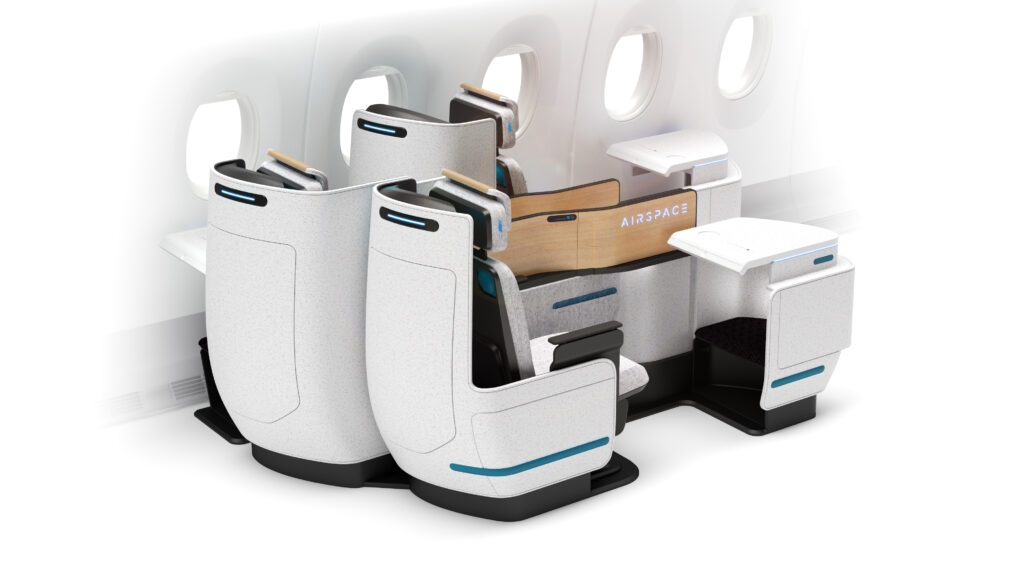
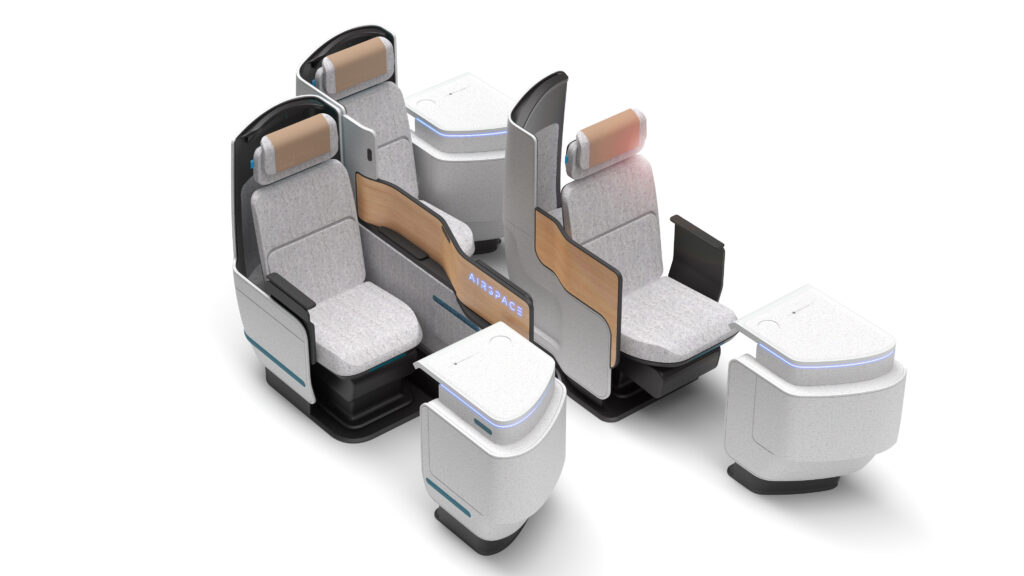
Ingo Wuggetzer, Vice President Cabin Marketing at Airbus sums up: “The seats represent one third of the cabin weight. Therefore [the] number one priority is to reduce the current weight of the products, followed by a more efficient seat layout and last, but not least, a new design philosophy: parts you can repair and with material that you can re-use or recycle.”
Elina Kopola, Co-Founder and Director of the Green Cabin Alliance (GCA) adds: “To move away from a linear process of ‘take, make and dispose’ to a ‘waste-free’ regenerative process will be the next big impact for our industry. It will take huge shifts in systems thinking for many industries, including our cabin interiors industry, to achieve this.”


Essential to realising this goal will be harnessing data and tracking the impact of the choices made across seat development and lifecycle. Gary Doy, Managing Director of Doy Design, explains: “One of the core challenges is we have to understand and qualify the positive impact we can achieve by making certain product, operational and business choices for our future aircraft seats.”
Recaro Aircraft Seating regularly performs life-cycle assessments on its products and CEO Dr Mark Hiller says: “From supply chain to the final assembly line, companies must analyse each part of their value chain to ensure all practices are sustainable. Simply focusing on the product’s weight during flight will fall short of many sustainable goals.”
Materials innovation
One outcome of Recaro’s life-cycle assessments is the R Sphere seat concept. This was created with lightweight and recyclable materials such as cork, wood, fishing nets and cactus with the goal of developing a model to collect and track feedback that will help Recaro make its future products more sustainable.
Hiller says: “The R Sphere raises awareness that aircraft seating and sustainability aren’t necessarily mutually exclusive. Seats that are designed with disassembly and recycling in mind will accelerate our journey towards a sustainable future.”
Over the next few years, we can expect to see the seating sector increasingly focused on innovating materials, manufacturing and business methodologies that will support a circular economy transformation.
Recycled leather specialist Gen Phoenix, in collaboration with aircraft seat cover manufacturer Sabeti Wain Aerospace, says it has developed aviation’s first fully closed-loop circular dress cover that can be completely recycled at the end of its life into new dress cover material.
Gen Phoenix Chief Innovation Officer and General Manager Seating, Nico den Ouden explains: “Through a take-back programme Gen Phoenix will collect and recycle the airline’s waste to create the next generation of aircraft seat covers for their customers, with no compromise to performance or customer experience.”
Alternatives to fossil fuel-based materials are a critical area of focus. Designer Daniel Clucas, Founder of Studio ID and a member of the GCA Leadership Board, observes that work on bio-based, plastic-free, lighter weight and recycled materials is underway in almost every sector.
He says: “There are now databases available containing material sustainability information – allowing appropriate choices to be made at the design stage.”
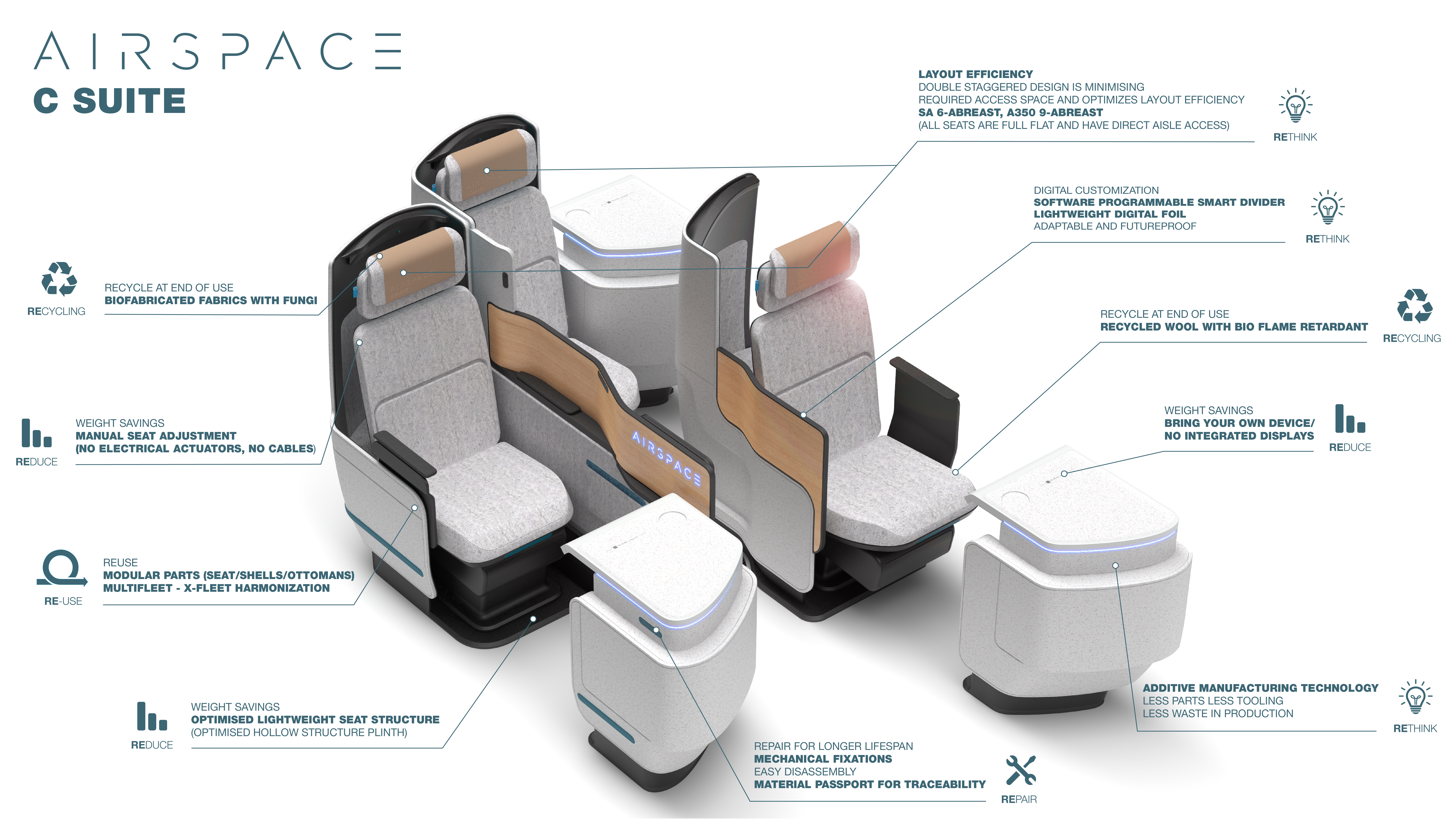
Airbus Head of Creative Design, Paul Edwards agrees: “In the next few years we hope to see more bio-based materials implemented into seat covers and structure….For example, in our C-Suite [business seat concept] mock-up we investigate the use of algae as [a] base material for the seat foams.”
He goes on to say: “Other technologies that are not far from being a reality are 3D printing and 3D knitting. Both allow our industry to reduce the amount of waste generated in the production phase, but also contribute to the reduction of weight, which is essential for the aircraft operation phase.
“Beyond seat design and materials, we need to leverage the power of digital solutions such as Internet of Things [self-diagnosing] devices to make seat maintenance more efficient, and high bandwidth WiFi onboard that would eliminate the need of installing in-seat inflight entertainment (IFE) in some operations.”
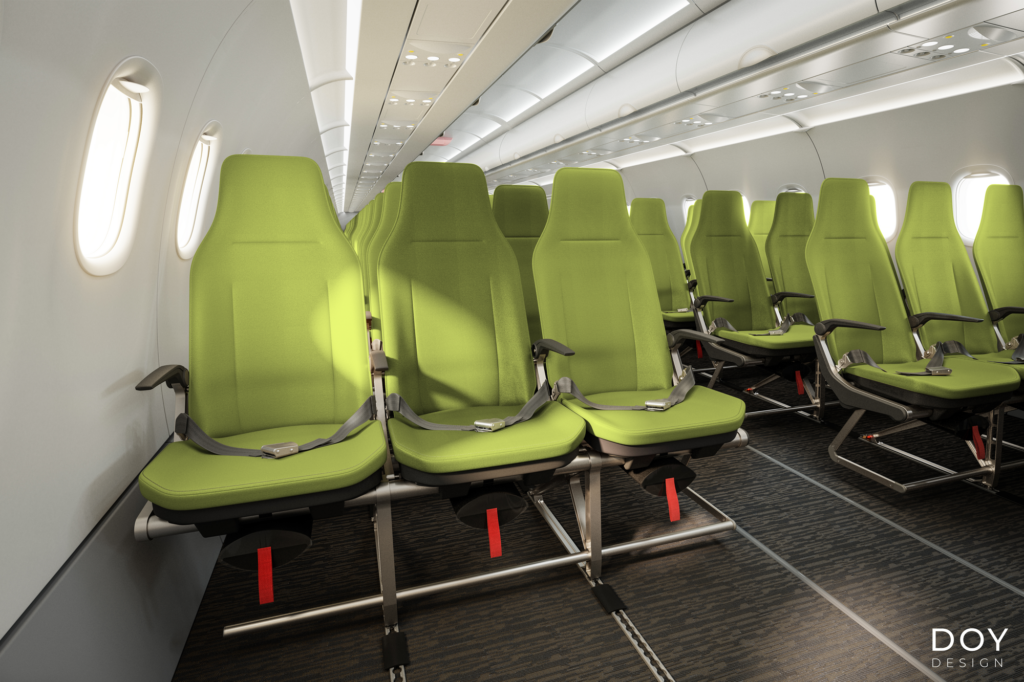
Existing materials such as aluminium, can also play “a significant role” in the next generation of seat according to Gary Doy. Doy Design’s 6.6kg Ultra Slim Low Carbon economy seat concept reduces the carbon footprint of its material content by 70% through the inclusion of recycled materials such as the aluminium monocoque backrest.
“Aluminium is readily recycled,” he says, “And we use high quantities of common aircraft grades in the production of seats today, especially for the primary structure….Defining a path for recycling, re-certifying and re-using aluminium in the aviation sector will make a difference.”
Ingo Wuggetzer at Airbus says circularity and material efficiency must be further facilitated by reducing the number of materials used. He adds: “Another aspect is modularity and space efficiency. Seats must be suitable for different aircraft types so [that] passengers have a consistent experience and airlines reduce the complexity of their parts inventory and lower development effort overall.”
Simplifying business class
Business class seating by its nature is heavier and feature rich, but the environmental impact can be lessened using similar principals. Noting that Recaro has one of the lightest business class seats on the market, Hiller explains this is achieved by keeping part numbers/variants to the minimum and using high performance composites such as carbon/glass fibre components for larger surfaces.
He adds that a modular design approach “enables seamless replacement with lightweight options or removal of unwanted features…thereby reducing the overall weight of the seat.”
Simplifying some functionalities helped Airbus offer the potential of significant weight savings for its C-Suite business seat concept. Paul Edwards observes: “We envision a business class seat that is mechanically actuated and that doesn’t have an in-seat IFE screen. With such an approach we could achieve weight savings of around 30% compared to benchmark seats.”
He continues: “Beyond the seat structure, we would like to ensure all materials we selected are recyclable or biodegradable. Those features combined with digital customisation have a great potential to improve the environmental footprint of business class seats.”
Innovating circular and regenerative products implies an equally strong emphasis on innovating business models. The GCA’s Elina Kopola explains: “The challenge…is to establish a new economic framework for this regenerative process. For example, we need to establish [a] robust supply chain for recycled raw materials for many substrates like polymers, aluminium, and textiles.”
That means understanding how to capture the materials as they come to the end of their useful life to circulate into further incarnations.
Gary Doy says: “This moves us towards material passports and accountable owners who have a responsibility and commercial interest to recycle and make the best use of these resources.” He concurs that focusing on the end-to-end lifecycle of seats and materials, as well as measuring the overall cost of the system, will drive more sustainable processes.
“We need to move the incentive away from a revenue system reliant on spare parts and heavier cost optimised solutions to one focused on reducing the operational impact of the seat.”
The move to greater circularity and sustainability will be an ongoing and iterative process. Changes to seating are probably going to be more disruptive in terms of money and time resources than the business and airline customers would like, but far from fearing these disruptions, we need to start making them part of the business proposal at every level.
And, if we return to the idea that seating is a microcosm of the business as a whole, disruptions will be likely to be going on throughout the business. Managing this plethora of change is, inevitably, the nature of modern aviation.
Sustainable seating – the passenger’s experience
As the focal point of contact between the passenger and the aircraft, the seat is the most immediate way for travellers to visualise and fully understand the environmental impact of their travel choices. In the future that may mean rethinking the offer as well as streamlining the space.
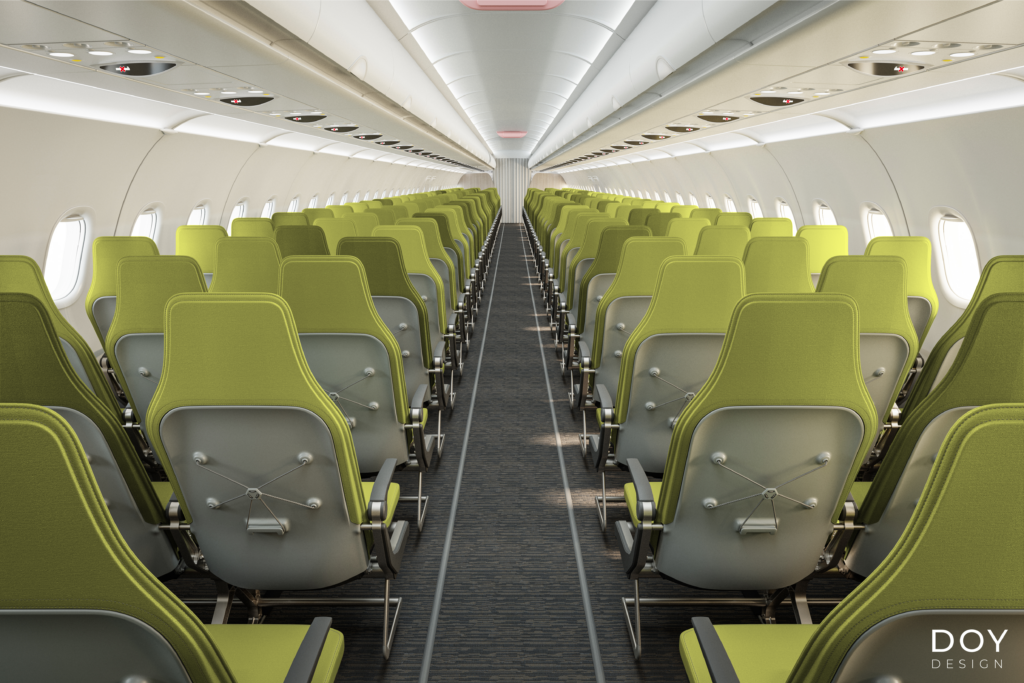
Gary Doy of Doy Designs predicts: “We could see airlines delivering comfort and space without the frills of inflight meals and other buy-on-board products that add weight.” His vision removes the meal tray table to be replaced by a simple docking system for carry-on meals purchased in the terminal.
He adds that taking out the galley, associated carts and buy-on-board would not only provide additional weight reduction, it would free space for a larger rear lavatory to support passengers with restricted mobility.
Modern luxury travellers are prioritising conscious consumption and increasingly looking for more sustainable ways to travel without compromising passenger experience, according to Gen Phoenix’s Nico den Ouden. “We believe that sustainable solutions will become the luxury choice of the future,” he says.
GCA’s Daniel Clucas adds higher budgets for business cabins provide scope for innovation. “Generally more sustainable materials and processes are still more expensive, and so there’s an opportunity in business class to push the boundaries and be more experimental.
The same principles apply as in economy, and you could argue that fewer materials, simpler design with less complexity can also be viewed as more luxurious – think residential interiors or even car interiors.”